One of the things we love most about KaiNexus is that we’re a technology company providing a continuous improvement platform that doesn’t subscribe to any particular methodology. That means we have people that are doing six sigma, lean, and kaizen. The result is that we see people coming up with novel ways of using KaiNexus that we never imagined. One such practice is using KaiNexus to support a class.
Why would you want to use KaiNexus to support your class?
Imagine you’re teaching a seven day Lean class spread out over the course of two and a half months to about fifty students. The course is a continuing education course for adults, who – studies show – learn better when they actually do what they’re learning about. As such, you chose to teach the class by having each student identify two opportunities for improvement in their workplaces using Lean principles, and then using the Lean practices you taught them to resolve them.
Students work on their projects independently throughout the semester, while you monitor their progress remotely and provide coaching along the way. That’s a tall order, but can be made easier if your class is managed in the KaiNexus continuous improvement software platform.
KaiNexus Allows You to:
- Monitor student projects remotely.
You probably won’t be onsite for the entirety of those two and a half months, but your students will still be working when you’re not there.
KaiNexus allows you to monitor their progress as they work through their improvements without being physically present. This saves you time, and gives your students the reassurance that you are looking out for them.
- Provide real-time feedback to students.
One of the most frustrating experiences a student can face is to have worked for weeks on a project only to attend the next class and be told that their work had gone wrong almost immediately.
With KaiNexus, you are able to provide instant feedback to your students. If you see that someone is veering off-track, you can reach out to them and provide coaching so that they don’t waste their time and get fed up with the whole process.
- Need less meeting time.
It’s hard to get everyone involved in the class in a room at the same time. It’s much more efficient to let your students do most of their work remotely and communicate via KaiNexus.
Additionally, in a traditional Lean course, much of the meeting time will be spent rehashing everyone’s progress since the last meeting, rather than talking about next steps and ways to improve. With KaiNexus, everyone can be kept up to date on each project so that meeting time can be spent much more efficiently.
- Prove a class ROI.
Across almost every industry today, organizations are on journeys to implement culture of continuous improvement and innovation, and so are turning to Lean coaches and consultants. But for many, the question still remains as to the true impact of continuous improvement and whether training can help drive and sustain those results.
KaiNexus allows you to accurately measure the ROI of your class and of continuous improvement in general. If you can point to a quantitative measure of the results of your course, you become a much more desirable coach.
- Create a permanent record of who was part of the class and what work they did.
The most obvious benefit here is for you as a teacher. KaiNexus is an easy means of record-keeping. By having everyone’s work (and the results of that work) stored in one place, you can quickly see a summary of your students’ efforts.
The other benefit is to your students. After identifying opportunities for improvement, acting on them, and resolving them, it’s critical that leaders provide sincere and meaningful recognition for everybody who participated in the process. KaiNexus helps you recognize employee contributions through online badges, and by prompting leaders to recognize employees who have participated in improvement work.
Actual Results from a Class Taught in KaiNexus
The above hypothetical was based on a real scenario:

The 47 students in this class identified and resolved 96 opportunities for improvement, with 96% resulting in an improvement in finances, quality, safety, and/or satisfaction. Here's the breakdown of the impact their opportunities for improvement had:
-
$1,686,559 recurring cost savings
-
$140,672 one-time cost savings
-
$306,617 recurring revenue generation
-
18,138 hours saved per year resulting in $570,658 of labor soft savings
-
67 improvements to quality
-
35 improvements to patient and staff safety
-
98 improvements to patient and staff satisfaction
A real opportunity for improvement from a class taught in KaiNexus:
Microfiber Floor Cloths and Floor Mop Inventory Control
- Problem Description
"The Housekeeping department introduced new cleaning procedures in 2010. The procedures require that cleaning staff only use fresh cloths and floor mops for each individual patient room. In addition, all isolation cleaning procedures require multi-step cleaning procedures. Each of these steps requires separate fresh supplies. At the time of the introduction of these procedures estimates of additional supplies were done and budgets adjusted.
Over the past three years the costs of maintaining adequate supplies has continued to increase. An analysis was recently performed which demonstrated as much as 17% of the daily supplies were not being returned. The costs of lost supplies has risen to $39,000 per year. Faced with increased budgetary pressures the department must reduce waste and unnecessary waste."
- Implemented Solution:
"The Housekeeping department has implemented the cleaning cloth and floor mop racking system the week of October 28th, 2013. Each of the day shift employees have had their work route analyzed by their section manager to establish their daily consumption needs taking into consideration the number of patient rooms, terminal discharge cleanings averaged per day and current cleaning protocols in place. See attached protocols.
A typical Housekeeping attendant will require 25 – 40 cleaning cloths and 20 – 30 floor mops per day. At a unit cost of $7.90 - $9.25 per floor mop (depending on the model) and with a life cycle of 300 washes, it is imperative that the inventory of this supply item is managed. By establishing the amount of each item the employees receive each day and randomly auditing their returns, we can ensure an adequate daily supply and reduce additional costs from replenishing supplies sooner than budgeted due to supplies not being returned after each day."
- Impact:
- $9,000 annually-recurring cost savings
- Improved staff satisfaction
- Improved quality
For more technical information on hosting a class in KaiNexus watch this free webinar:

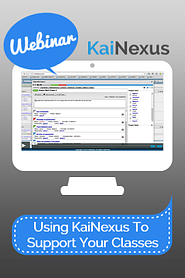
Duration: 30 minutes
Topics: Continuous improvement software, KaiNexus
Hosted By: Greg Jacobson
-
How to set up your classes in KaiNexus
-
The benefits of using KaiNexus to support your classes (including communication, remote monitoring, and reporting class ROI)
-
Real customer example of managing a class in KaiNexus that resulted in over $2.7 million of financial impact